acespicoli
Well-known member
Specs are from independent testing facilitiesI wouldn't trust a thing Spiderfarmer tells ya mate they have been lying about specs since they started!
American National Standards Institute - ANSI Home
The American National Standards Institute - ANSI - facilitates and corrdinates the U.S. voluntary standards and conformity assessment system.


RoHS Directive
Discover EU rules on the restriction of hazardous substances in electrical and electronic equipment (RoHS in EEE).
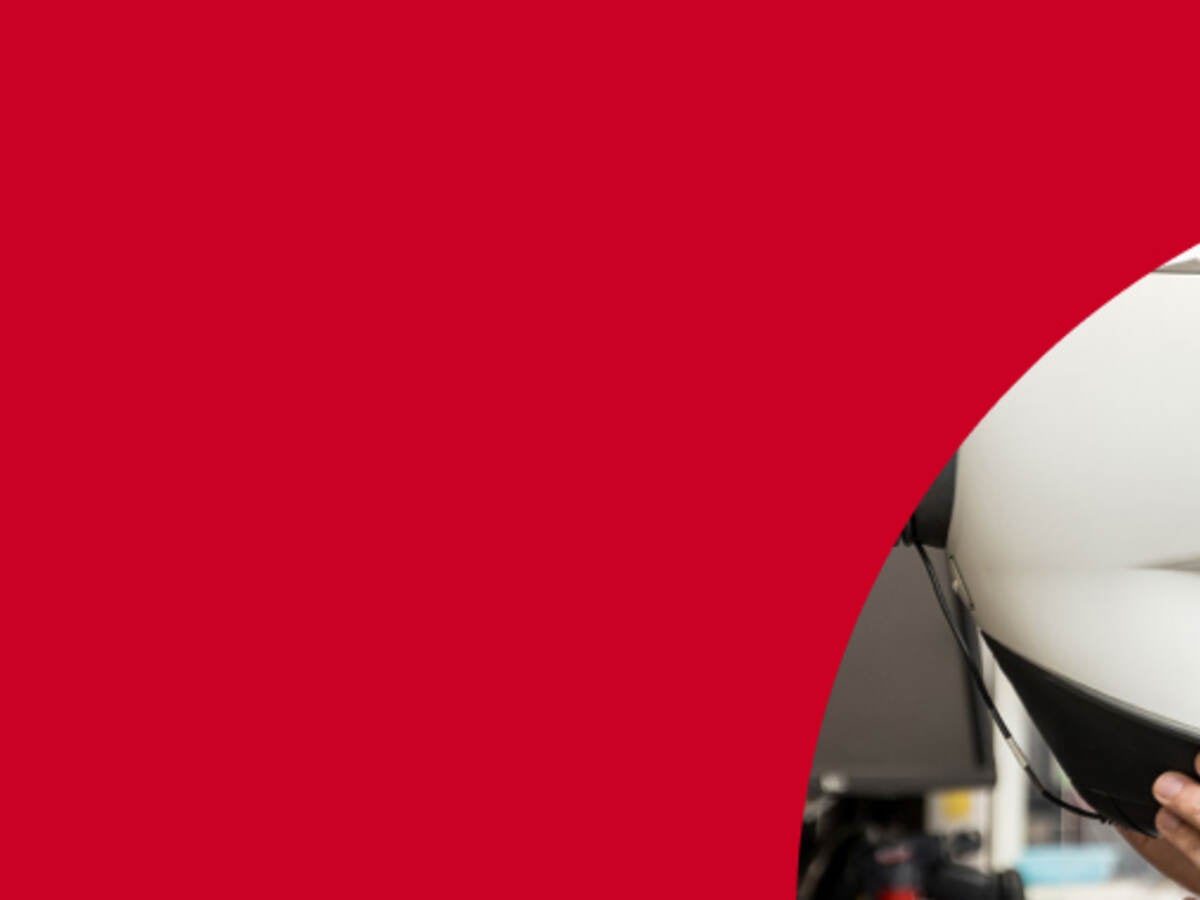
UL Empowering Trust®
UL is a global independent safety science company with more than a century of expertise innovating safety solutions.
The spreadsheets have all the LED specs from all the industry manufacturers and certifying tech companies
We just need to look at what diode at what voltage and how many diode's
Sure there are many that list the apex, looks better than the average
Last edited: